Ovako’s tubes and hollow bars are used when there are stringent demands on the material, such as within the rolling bearing, automotive, hydraulic and manufacturing industries.
As a service to our customers, we have a standard tube program offering smaller order quantities and a shorter lead time than we normally require for a production batch. Ovako has two such standard programs. The bearing steel program covers roughly 350 tube sizes from OD 50.6 to 243.5 mm, and the Ovako 280 hollow bar program that covers microalloyed steel hollow bars in grade Ovako 280 based on the standard EN 10294. Within the Ovako 280 hollow bar program, we keep roughly 250 dimensions in stock from OD 30 to 242.7 mm.
Both the bearing steel tubes and the Ovako 280 hollow bar program are based on tight machining allowances. For each item we can provide a guaranteed finished turned size for either inner or outer chucking. Both have the tubes stocked at our mill as well as at some of our sales companies and appointed distributors. In addition to the bearing steel program and the Ovako 280 hollow bar program, we supply tubes in all Ovako standard steel grades.
Reducing global CO2 emissions demands smarter product solutions and requires rethinking on many levels: more performance benefits per kilogram of product, less raw materials, and substituting fossil fuel energy sources with primarily fossil-free electricity. Read more about Ovako’s path to carbon neutrality


Hot-rolled tubes, cold-worked tubes
In most cases we sell tubes for a specific application. To support this, all tubes are delivered with a guaranteed finish machined size. Since we produce our products as close to final clean machined components as possible, our entire size range requires minimal machining, with inner or outer centering on a maximum part length of 2.5 x OD. For longer parts an extra allowance is calculated.
Tolerances
The level of a machining allowance is calculated from the tube tolerances. To support our small machining allowances, Ovako has very tight tolerances across the entire size range, both with regard to outer diameter and wall thickness, as well as other parameters such as straightness and ovality. In practice, this means less machining and better yield for the user, resulting in lower component production costs.
The maximum deviation from the straight line is 1 mm on a gauge length of 1,000 mm and the maximum out of roundness is 65 percent of the total outer diameter tolerance.

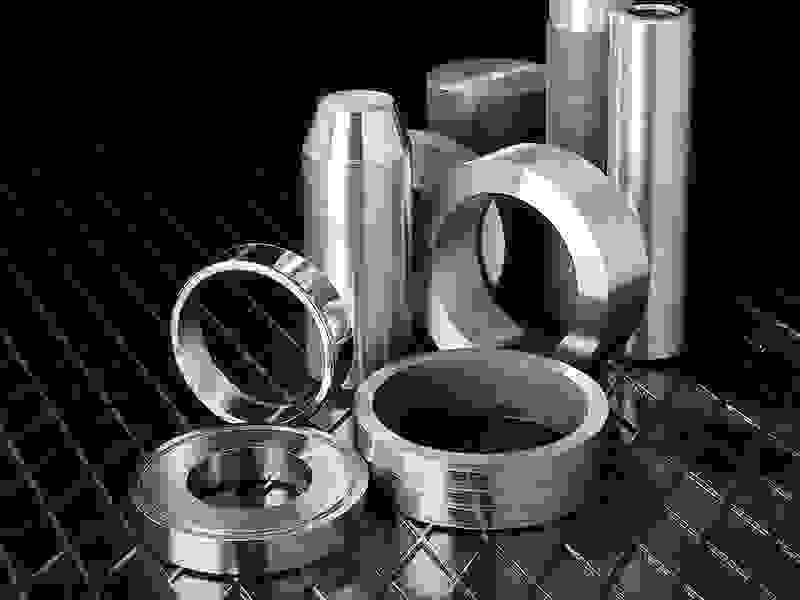
Pre-components from tube
An ever-increasing trend in industry is to buy premachined or completely finished components. Ovako has recognised this and invested in the resources required to manufacture components, in particular the supply of cut blanks. Our production systems are designed to respond to both short lead times and product optimisation to satisfy our customers' requirements. The equipment is flexible and able to handle small quantities of short runs as well as long-run mass-production batches. With broad experience in different types of applications, and a thorough knowledge of our products, Ovako is uniquely able to find an alternative solution best suited to meet individual requirements.
Production program
The diameter, tolerances and surface finish of components are the same as those stated for the full-length tube.
Outer diameter: 25 to 254 mm
Lengths: 10 to 5,000 mm
Cut rings can be delivered shot blasted on request.
Deviations from square cut are within the tolerances above, albeit limited to the following values:
- Deviations from square cut are to be a maximum of 1.0 percent of OD
- Deviations from square cut determine the tolerance when the deviation exceeds the tolerance


Packing
The components are supplied, packed in collared pallets, arranged randomly or stacked, either unprotected or wrapped in waxed paper or plastic shrink-wrapped, depending on the method of transportation. Customer specific packing specifications can also be met.
We made it! But we are still not satisfied
What a journey! It took years of hard work to make our steelmaking operations more sustainable. In 2022, we went carbon neutral in all operations. But we´re still not satisfied - our journey towards steel production without CO2 emissions continues.
Read more about our path to carbon neutrality
