In the tough environments of the mining, construction and agricultural industries, wear is a fact of life. However, with clever design and specification of wear resistant WR-Steel, engineers can design machines to withstand challenging conditions for longer. As a result, operators will get more life from their machines, reduce repair and maintenance spend, and avoid downtime.
There are four wear mechanisms: plowing, cutting, wedge formation and cracking (also known as brittle fracture). However, these differ, depending on the application.
Therefore, a component like a bolt on edge (BOE) on a wheel loader would experience plowing and cutting from the action of pushing the edge into the ground. In comparison, a down-the-hole (DTH) drill bit will be hit by millions of airborne particles, causing cutting and brittle fracture.
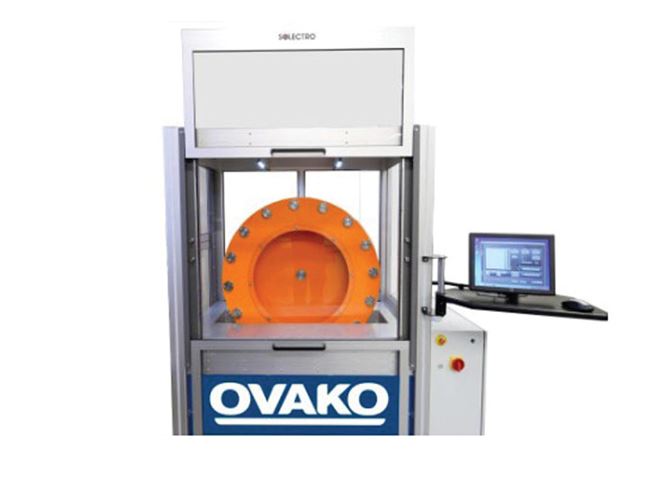
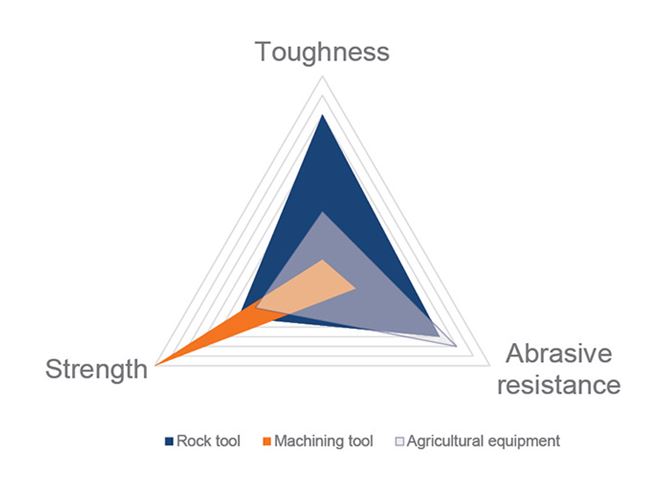
Measuring the wear resistance of steel
Armed with knowledge on how wear happens in the field, we can help our customers identify a material (or materials) to resist the specific combination of wear mechanisms that their tools will face.
We concluded that wear resistance comes down to three mechanical properties:
- Strength, as measured by hardness, resists the plastic deformation of plowing and cutting.
- Toughness, measured with Charpy-V testing, resists impact loading from abrasive materials and therefore limits brittle fracture.
- Resistance to abrasive wear – this is important as materials with the same strength and toughness can show different wear resistance due to having different microstructures. Therefore we developed our own in-house test method called the Ovako WR-drum to evaluate this.
By combining our knowledge of the wear mechanisms in different industries with the three properties, we have been able to visualize the most important qualities required for real-world applications. These are mapped out in a property zone shown below as strength, toughness and abrasive resistance.
With this knowledge in place, we can work with customers to test and evaluate their needs and quickly suggest suitable grades of WR-Steel for their specific applications.
You can learn more about wear mechanisms, how they apply and our WR-Steel selection methodology in our Technical Report, Understanding wear mechanisms – the application technology behind WR-Steel.