In early 2022, Ovako´s steel mill in Hofors began looking at alternative solutions to address the growing challenge with the amount of magnesite brick that needed to be disposed of and sent for landfill. If they could find a solution to recycle the exhausted bricks instead, there would be many potential benefits. The result has meant a new approach to the smelting process, alongside several positive environmental aspects.
We have spoken with Mikael Bror, Purchasing Manager Raw Materials and responsible for residues in Hofors and Patrik Undvall, Technician Black Bar, to learn more.
A trial began by collecting the exhausted brick and crushing it to 0-3 mm. They were then added to the electrical arc furnace instead of being sent to the landfill as before. The innovative thought was that the brick would be able to replace the need for a large part of the Dolomite, which is purchased from England and otherwise needed in larger quantities. Samples from the slag was sent to LTU (Luleå University of Technology), to be able to confirm from an independent source that the addition of the crushed brick dissolved into the slag properly, therefore fulfilling the intended purpose.
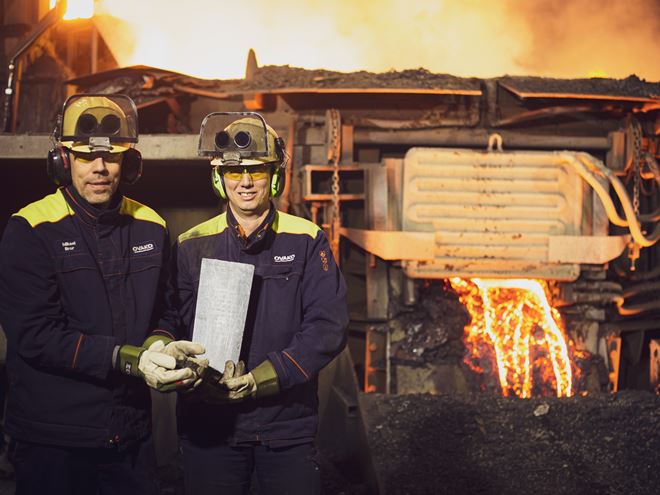
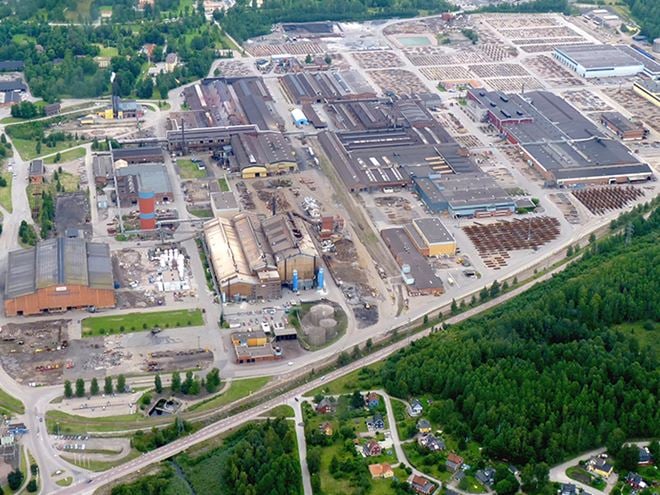
"It became clear pretty quickly after the test results, that we could build a good case for this. First of all, we are doing nature a favor in an environmental sense. Instead of depositing it at a landfill, we are reusing material that has already been excavated. Dolomite is an expensive and energy-intensive product to produce as well as to purchase, and we can now avoid digging out of the earth's crust for new material as well as having to pay for a high landfill / purchase price." Mikael explains.
The environmental impact of producing Dolomite is estimated to be on average 1100 kg CO2e / ton of Dolomite (source: Worldsteel). Every ton Dolomite not used by Ovako are therefore decreasing our emissions up streams in our own value chain by roughly 1100 kg CO2e. Another positive environmental aspect is that the long transport routes now are drastically reduced. The bricks are, compared to the purchased Dolomite, already in our dispensers and electrical arc furnace. The harmony in making use of the leftover bricks instead of depositing them in a landfill is well balanced, seeing that the volume “falling” in the process after consumption is more or less equal to the amount needed to be added in to each new batch. The implementation of this process alone will save an estimate of 900 tonnes of CO2e every year, further reducing Ovako´s already world leading low CO2 footprint.
A small amount of Dolomite will still be needed for the solubility of the slag, to protect the lining in the furnace. Without the proper balance there, the lining of the arc furnace wears down quickly, and naturally, we want to have as long a lifetime for the arc furnace as possible. Patrik Undvall, Black Bar technician, is responsible for ensuring that the chemical balance in the arc furnace is correct based on this new approach.
"The slag in the electric arc furnace is in equilibrium with the brick the furnace is lined with. When we add finely crushed brick, it has such a large surface area that it will dissolve into the slag faster than the lining brick, thus reducing the wear of refractory material in the electric arc furnace while reducing the consumption of dolomite." Patrik explains.
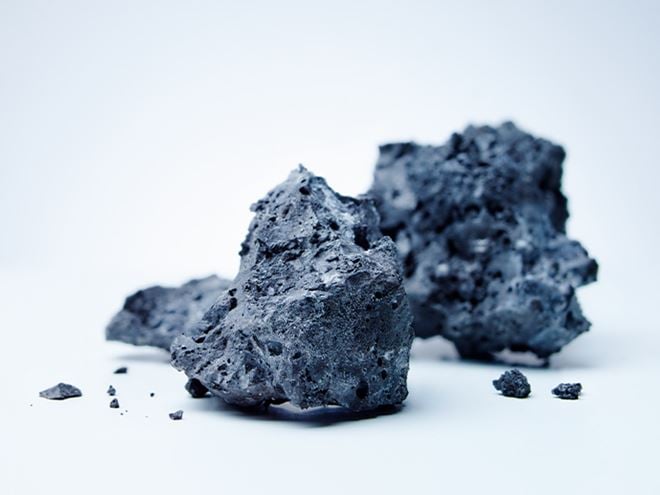
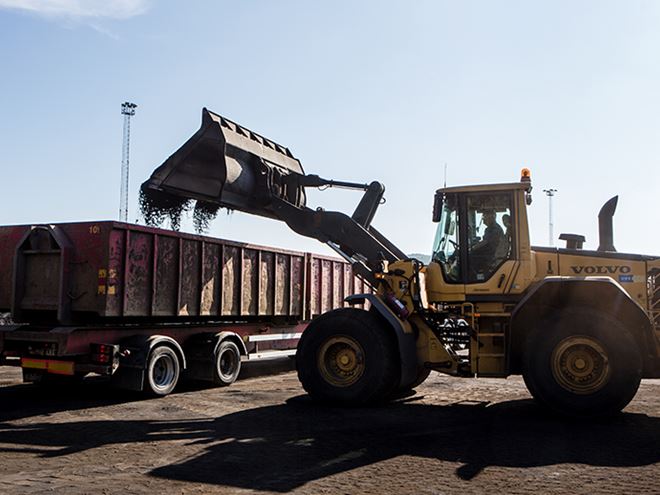
After clarification from the laboratory tests as well as Ovako´s own calculations were finished for how to get the right balance in the arc furnace, the process has continued on since. The same process is already implemented in Ovako´s steel mill in Smedjebacken and Imatra, and is now also included in Sanyo Special Steel's very own list over future potential projects!