As all industries drive to adopt a green agenda, while environmental legislation also becomes increasingly stringent, NiKrom III offers an innovative approach to the surface coating technology essential to provide hydraulic piston rods with protection against corrosion penetration and pitting of the underlying steel. This duplex coating, combining a nickel underlayer with advanced hard trivalent chrome (CrIII), is a high-performing, alternative to hexavalent chrome (CrVI), a substance included in the REACH directive.
NiKrom III integrates into existing production systems and ensures high durability, corrosion resistance and wear protection. It meets the stringent requirements for components like piston rods which are often exposed to harsh environments in hydraulic applications such as mining, offshore or chemical plant – see Figure 1. (to the right/below) NiKrom III is also ideal where piston rods are exposed for long periods of time, e.g. tailgate lifts, snow ploughs or ski lift systems.
Figure 1 – NiKrom III lift cylinder rods are ideally suited to mining equipment such as this Sandvik Loader when deployed in harsh conditions
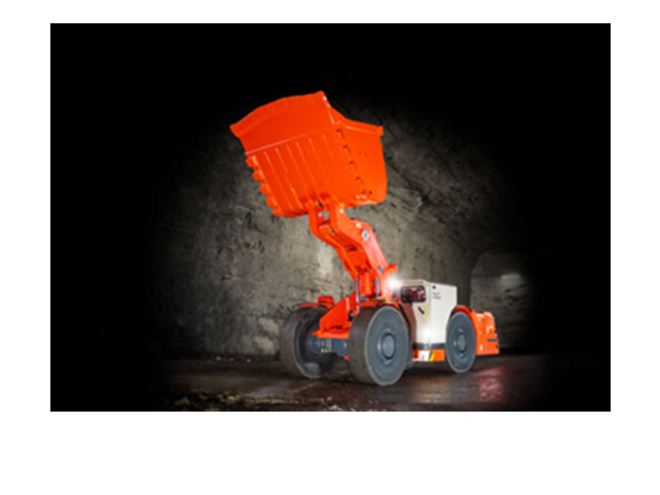
The process
At the heart of NiKrom III’s success lies the process developed in cooperation with leading companies in the chemical industry. To mitigate the potentially lower performance of the CrVI-free chemistry, we have utilized our extensive experience and knowledge in duplex nickel-chrome coatings. With this approach, we have been able to transfer the unparalleled corrosion resistance performance of our NiKrom products to the CrVI-free NiKrom III products.
The process requires careful control because of the sensitivity of the CrIII bath’s chemical formulation to contaminants. Maintaining consistency and reliability depends on precise oversight. The outcome is a highly durable coating.
The first demonstrators from a manually operated pilot facility were produced in Ovako’s Redon facilities in 2017, this is the French plant where we produce our nickel-chrome products. Since then, we have carried out extensive development of the process and chemistry. Production has also ramped up to a fully functional pre-series line able to produce bars up to 3m in length in diameters between 20mm and 140mm
A viable alternative to CrVI coating
For NiKrom III to provide a viable alternative to the CrVI coating it is essential that it can be used with existing hydraulic cylinder designs. NiKrom III has a similar surface structure, hardness and friction properties as standard chrome products, this makes it possible to use with existing sealing designs. Furthermore, NiKrom III can be applied on any Ovako Cromax steel base without additional heat treatment, so customers do not have to compromise on mechanical properties, fatigue life or ease of welding.
Successful trials with Sandvik - Proven performance in extreme environments
The adoption of NiKrom III has been well received by key stakeholders. One example is Sandvik Mining and Rock Solutions, a global leading supplier in equipment and tools, parts, service and technical solutions for the mining and infrastructure industries. Sandvik’s machinery operates in harsh mining conditions, often in remote locations, where reliability and uptime are critical to success .A fast-growing part of the business area's offering is solutions for automation and remote monitoring of equipment, which increases operational efficiency and process reliability. The mine automation systems cover all aspects of automation, from single equipment to full fleet control.
Sustainability is also a key focus for Sandvik. The company’s targets for reducing greenhouse gas (GHG) emissions have been validated by the Science Based Targets initiative (SBTi). With these targets, Sandvik commits to reducing absolute scope 1 and 2 GHG emissions by 50%, and to reduce absolute scope 3 emissions by 30% by 2030.
Sandvik Mining and Rock Solutions Load & Haul division recently started using NiKrom III cylinders on a variety of its mining machines having been introduced to the concept by Ovako Cromax’s partner, Wipro Infrastructure Oy. After discussions between the technical teams of both companies, Sandvik decided to launch an in-field testing project. The testing took place in highly corrosive environments, particularly in copper mines where the saline atmosphere accelerates corrosion. The results were impressive: while standard cylinders would typically show signs of corrosion over time, NiKrom III cylinders remained corrosion-free up to five times longer. See Figure 2.
The advantages of using NiKrom III cylinders are clear. By delivering these cylinders to customers, Sandvik is providing the best product solutions, significantly reducing service and repair costs. This is crucial for mining machinery where downtime is very costly.
Currently, around 20 machines have been equipped with the new NiKrom III cylinders, with more deliveries planned for 2025. Sandvik now offers NiKrom III as an option on selected cylinders, anticipating an increase in volume in the coming years.
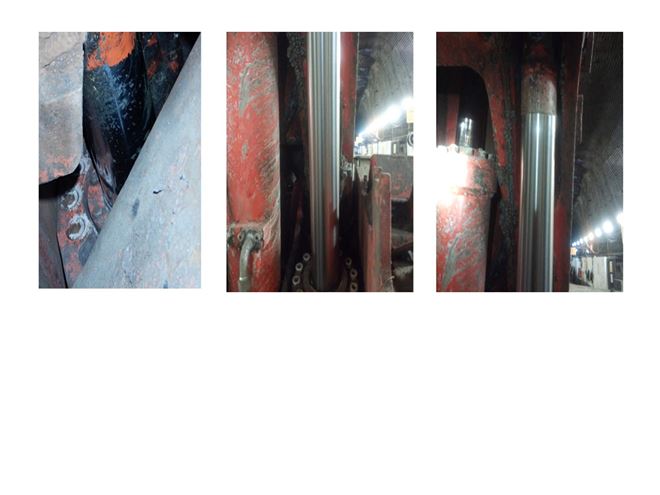
A sustainable vision
NiKrom III aligns with Ovako Cromax’s overarching sustainability goals. For example, attention is given to the carbon footprint in all steps in the production process from steelmaking via hot-rolling, transport, machining to plating. The final product has a carbon footprint 80% lower than the global average, and, on request, we can provide carbon footprint data on the article number level.
The road ahead
As industries using hydraulic equipment adapt to stricter sustainability regulations, Ovako can provide solutions to meet this challenge. NiKrom III is an additional piece in the puzzle that aligns with these evolving demands. The technology is ready to scale up to meet the needs of sectors like mining, marine, wind turbines, and coastal infrastructure, all of which benefit from its properties.
It is important to remember that NiKrom III isn’t just an alternative to CrVI, it can also be a problem solver in niche applications. It shows how innovation and sustainability can work in tandem to deliver a significant return on investment.