Ovako has developed Hybrid Steel to merge the unique properties of tool steel, maraging steel and stainless steel into one high-performance steel grade that also offers the production economy of conventional engineering steels. This is made possible by the successful combination of alloy carbide and intermetallic precipitation hardening. The resulting Hybrid Steel offers eight key benefits:
1. High strength, especially at elevated temperatures
2. High-volume, cost-efficient production
3. High hardenability enabling low distortion
4. High cleanness and fatigue strength at elevated temperatures
5. Uniform properties with low microstructural segregation
6. High strength with good weldability
7. Excellent surface treatment possibilities
8. Good corrosion resistance
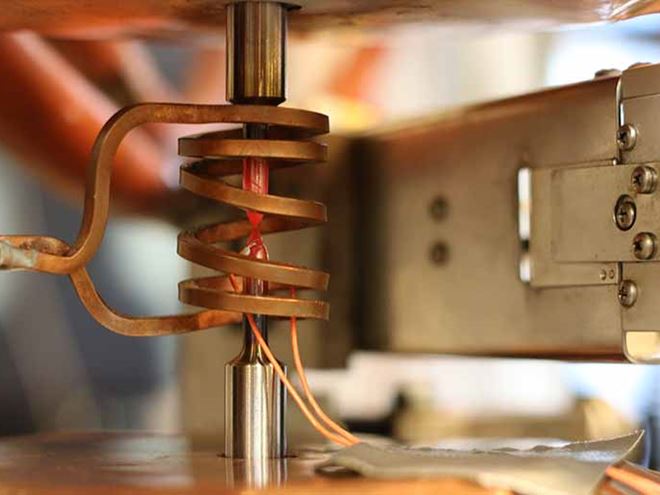
Figure 1 – Elevated temperature tensile testing of Hybrid Steel.
One of the most attractive advantages of Hybrid Steel is that at temperatures around 500° it has three times the yield and tensile strength compared to engineering steels tempered at 550°C. These properties are ideal for a wide variety of highly-stressed components, especially in engine and powertrain applications in the automotive industry.
Enhanced fatigue life at elevated temperatures
To ensure reliability and long life, engine and powertrain components must be able to sustain high loads in extreme conditions. Fatigue is generally the main life-limiting factor for any well-designed steel component. One of the most important factors for fatigue resistance is that the steel microstructure should not be weakened when exposed to the operating temperature and load, as this energy input causes the microstructure to degrade.
Hybrid Steel achieves its strength after high-temperature tempering which results in an extremely stable microstructure. Tests show that this produces a much higher fatigue resistance at elevated temperatures, and the effect is significant even at moderate increases in temperature.
A further advantage of Hybrid Steel is its low coefficient of thermal expansion and high thermal conductivity when compared to austenitic steels. These properties permit Hybrid Steel to resist thermal fatigue when used in thick section components.
Properties proved under test
Tests (see Figure 1) show that Hybrid Steel achieves a higher strength compared to standard engineering and tool steels after tempering at high temperature. Elevated temperature tensile properties for various conventional steels and two Hybrid Steel grades are shown in Figure 2.
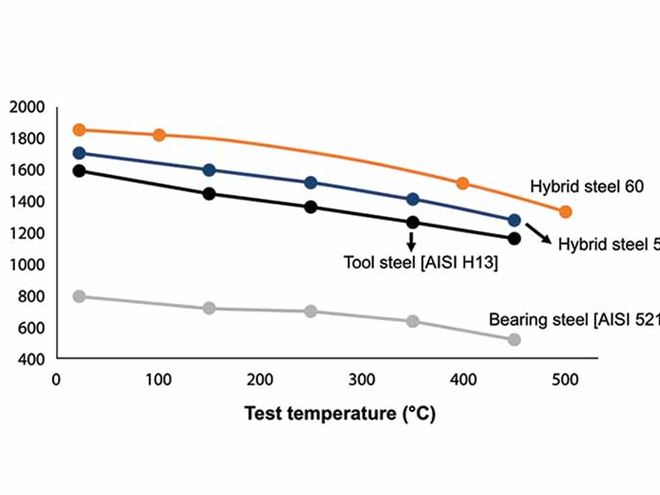
Figure 2 – Tensile test results at elevated temperatures, all steels tempered for use at 550°C.
Clearly, a high strength level is retained by Hybrid Steel and this is an essential characteristic of this new steel. For a component that experiences elevated temperatures, the first property considered is the strength during short-term exposure, such as in Figure 2. The short-time tensile properties are usually sufficient for the mechanical design of steel components for applications that involve short-term exposure to temperatures below 480 °C.
Surface processes
Another aspect of the temperature sensitivity of high strength steels relates to the various processes used to modify the surface of steel components. These processes might be applied to improve hardness, introduce compressive stresses, provide low-friction properties, increase corrosion resistance and more. In many cases the processes must be applied at an elevated temperature, which means that the underlying steel stands the risk of losing some of its properties. As Hybrid Steel reaches its full strength at elevated temperatures it therefore offers important benefits when surface processes are applied.
Creating new design opportunities
Andreas Rindeskär, Senior Application Engineer in Ovako’s Industry Solutions Development, has been investigating the potential uses of Hybrid Steel. He says:
“There are several interesting potential applications for Hybrid Steel, especially for components in or around an internal combustion engine that are subjected to severe operating conditions due to elevated temperatures, oxidation, corrosion and fatigue.”
One potential application is piston crowns. These are a particularly demanding materials application as they are subjected to high temperatures and high combustion pressures – up to 300 bar in some diesel engines. Typically, they need to be forged or cast in 42CrMo4 steel or aluminum. The high strength of Hybrid Steel at elevated temperatures and its good weldability could allow the design of lighter pistons that will make a significant contribution to enhanced fuel efficiency. And there is a knock-on effect that lighter pistons could allow the downsizing of other components such as crankshafts, for even lighter and more efficient engines.
Eliminating production steps
There is much more to Hybrid Steel than its exceptional physical properties. Because it achieves its full properties after tempering at temperatures with very low distortion, manufacturers will be able to eliminate production steps. This low distortion enables strongly reduced manufacturing costs, especially when grinding is an important consideration. As an example, a component could be machined to its final dimensions in a softer condition, followed by a simple heat treatment process to achieve full strength. This approach reduces complexity and costs.
With so many advantages and diverse applications the Hybrid Steel story is only just beginning.
Technical Report: Hybrid Steel® - the next step in steel evolution