When the British Army deployed its Warrior Infantry Fighting Vehicles in active service they faced a particular risk from improvised explosive devices (IEDs). To provide additional crew protection these vehicles were retro-fitted with additional armor. However, the added weight caused them to ride lower to the ground, which increased the risk to the crew and reduced off-road maneuverability. Could Tinsley Bridge provide a solution?
At the time, the vehicles were using steel suspension torsion bars based on standard spring grades, Due to the British Army’s urgent need, a higher-ride solution would have to be fast to implement and require minimal changes to the vehicles.
Tinsley Bridge engineers decided to develop a torsion bar with slightly wider dimensions to replace the standard steel suspension torsion bar. However, because the standard spring steel grades used in torsion bars is susceptible to inclusions and other impurities, Tinsley Bridge needed a cleaner steel that could also be heat-treated to a higher stress level. So the company turned to Ovako’s Imatra mill, which was able to produce a clean, high-strength steel modified to meet Tinsley Bridge’s specifications.
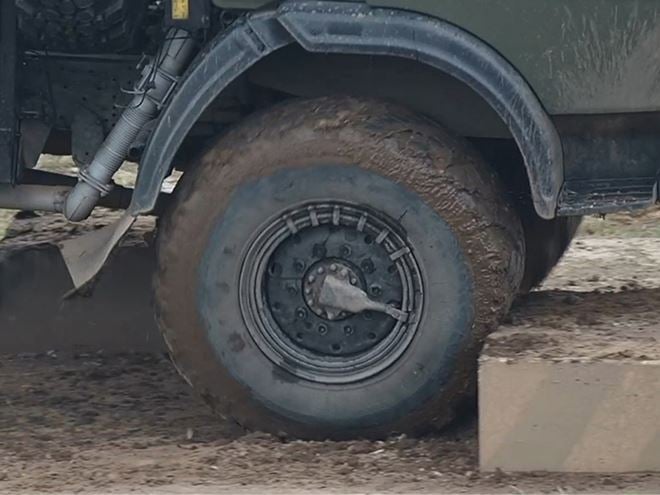
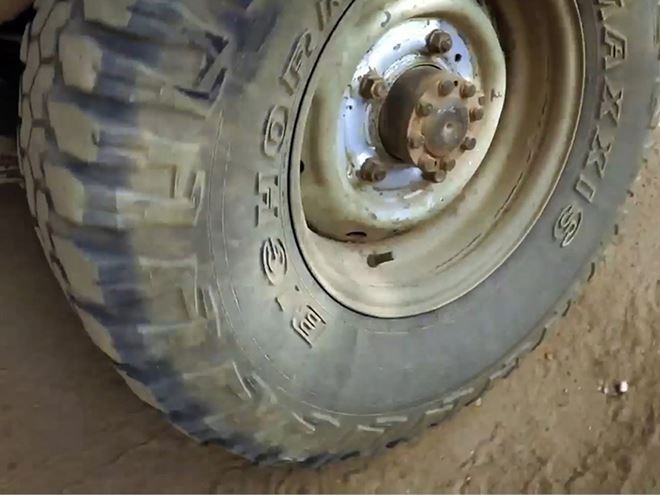
Development and testing of the higher-riding vehicle with the advanced torsion bar was completed in less than five months – a time frame that also included extensive field trials. The result was improved crew protection and increased cross-country mobility.
Solutions
- Cleaner high-strength steel with fewer impurities
- Torsion bar with higher stress level
- Modified to meet Tinsley Bridge specifications
When Ovako’s spring steel is delivered to Tinsley Bridge, it un-dergoes extensive processing. For example, the stabilizer bars, which are delivered already cut to length, have their ends upset forged and heat treated and quenched to maximize the steel’s strength. The bar is shot-peened for surface resilience before it is rust-proofed.
All these processes were streamlined to fulfill the end-user requirements.
Today, as Tinsley Bridge continues to invest in improving its high-stress torsion bars for military vehicles and stabilizer bars for trucks, Ovako regularly reviews its own efforts to improve the strength and high-load capacity of its steels.
Benefits
- Improved strength and high-load capabilities
- Ability to provide a fast response
The Minister of Defence praised the efforts of Tinsley Bridge in developing the advanced torsion bar, acknowledging the versatility of the Warrior vehicle, its good mobility and high levels of protection for its crew.
This is one example where Ovako has helped support Tinsley Bridge. In fact, Tinsley Bridge, which spun off from British Steel in 1987, and Ovako have had a mutually beneficial 20-year relationship.
Always seeking a competitive edge, Tinsley Bridge is currently testing Ovako IQ-Steel, an extra clean steel expected to support and increase the strength of the high stress torsion bars and high stress stabilizer bars while lowering the weight, according to Mark Weber, CEO of Tinsley Bridge Ltd.
Because Ovako has a wide range of experience from other industries the company has been able to bring that to bear on new ideas and innovations, he added.
Read more about Tinsley Bridge