People development is an area that has grown at Ovako in recent years and many initiatives and projects have been initiated and already carried out successfully. Leadership programs, Young Professional network and competence exchange programs are just some examples of initiatives that have been relaunched during 2022.
As an international company, we want to find ways to encourage two-way sharing of knowledge, even though we are 8,000 km apart. That’s why we’re establishing this Competence Exchange program with our owners Sanyo Special Steel and Nippon Steel Corporation. Ovako employees in the Nordic region can get the opportunity to travel to Japan for up to three weeks, or possibly longer for R&D projects.
Sweden and Japan both have cultures with long histories in steelmaking. By sending Ovako employees to Sanyo Special Steel, they’ll learn first-hand how our Japanese colleagues run operations. And by going in pairs, they’ll be able to discuss and reflect on their learnings in the evenings.
Jimmy Gran, VP and Head of Product Unit Black Bar Business Unit Hofors-Hällefors and Kari Välimaa, VP and Head of Product Unit Steel & Rolling, Imatra are two colleagues who have just returned from the exchange program. We ask some questions to Jimmy and Kari:
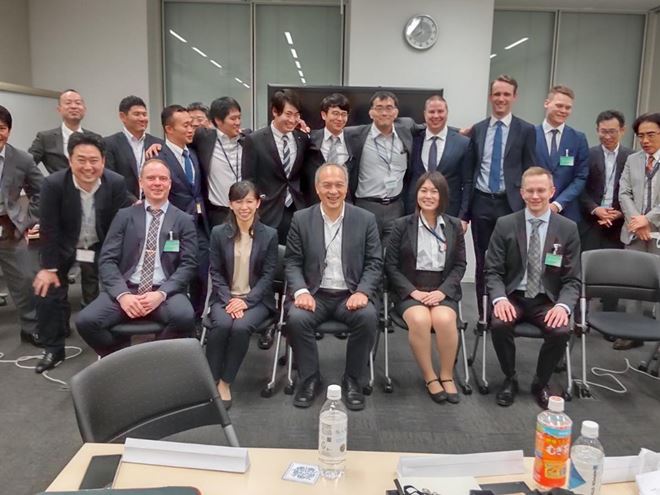
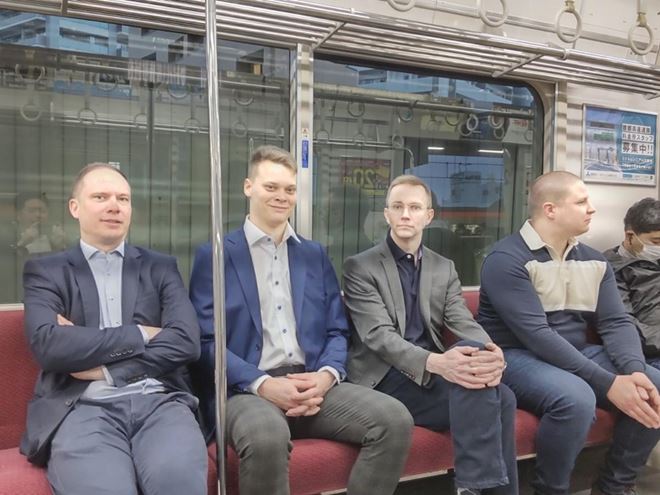
Tell us more about the exchange program and was it like you had expected?
The approach was quite ambitious from our side in the sense that we had a special interest in the Japanese way of working beside the obvious technical topics. One thing that we immediately noticed was the detail level of our visit plan both to Nippon and Sanyo. And in that way, we managed to include as much as possible into the visit program and we also got an insight into the most elemental thing about Japanese way of working – extensive and detailed planning!
Why do you think you were chosen to go to Japan?
We have both had a lot of contact with our Japanese colleagues the past years. One other thing is that our respective responsibilities (steel mill, billet mill etc.) – Black Bar production have an equivalent at both Nippon and Sanyo – hence the topics for discussion etc. are easy to identify.
What did you both contribute to the program?
Initially we suggested some topics of special interest. Our most familiar fields of expertise are on steel mill and casting, so naturally exchange of information and discussions with Japanese colleagues was easiest in these fields. And beside the technical points I think we both highlighted the “Japanese way of working”.
What are the main differences working-wise comparing Sanyo and Ovako?
You can find several differences. However, the difference that we see influencing the performance most is the long employment time at the same company in Japan. This brings a completely different continuity to the work compared to most other countries. Here we think that Ovako´s ambition to “attract and keep” employees are important initiatives. One other thing is their extensive planning work of more or everything that concerns the company. We can learn a lot from that approach, especially in the work concerning safety and risks besides typical engineering tasks.
What memories to you bring back?
A lot of memories, but the memory of their fantastic hospitality and the good discussions will stay in my mind for a long time. The participants in the exchange program showed a strong sense of mutual interest in learning from one another. It was a delightful discovery that there were always more topics of interest for discussion than there was time available on the agenda. This is good for the future of the exchange program, as it provides many opportunities to continue the exchange of knowledge and ideas.
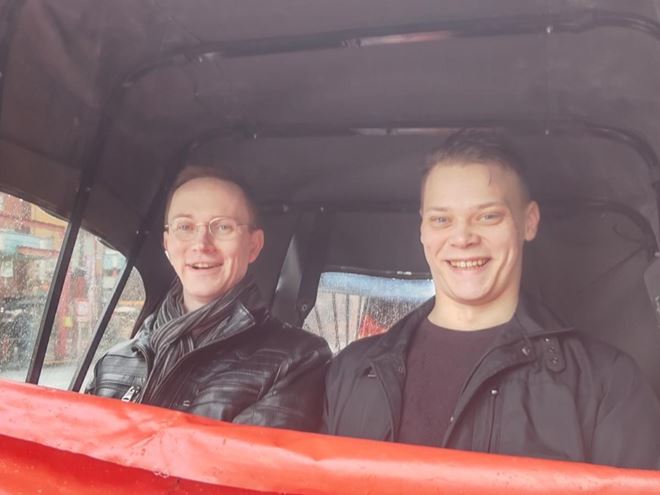